Abstract
- The pandemic has made it largely impossible for external staff such as specialized engineers or technical consultants to enter steel plants for their vital work
- New ways to continue technical support had to be found, facilitated by creative modes of service delivery as well as the newest digital communication technologies
- Steel Hub found from its own technical consulting work that remote support models led to unexpected benefits such as increasing operators’ capability for data-driven plant management
Can steel plants be managed remotely?
The pandemic accelerated trends that have been occurring already before it started, such as cashless payments, online shopping and remote work. Digital technology is an enabler of these trends. Remote work implies that office staff can attend online meetings just as easily from home as from their workplace — and meanwhile keep safe. Office-based “white collar” work is regarded as most suitable for such remote work arrangements. How about technical experts’ work though, for instance in steel plants? Surely engineers managing complex technical environments such as an electric arc furnace or blast furnaces need to be present on-site?
Although this used to be the case, it is now no longer entirely true. Long before the pandemic broke out, manufacturers had been investing in technology that enabled a reduction in the number of staff required to be present in the plant. This has helped them to improve productivity and increase competitiveness. This is demonstrated, for example, by Voestalpine AG’s plant near Vienna, which can produce 500,000 tons of steel wire a year with just 14 employees. The same mill in the 1960s would have required as many as 1,000 workers to produce a similar amount, albeit of lower quality.1
Among the indispensable jobs in direct association with technical plant management that remain, the bias is geared heavily towards the monitoring and maintaining of automated systems within smart factories, rather than manual labour carried out in the plant. Digital technology, when used innovatively, allows many of these jobs to be performed remotely. Steel plant operators, like their office-based counterparts, can also leverage remote work to manage operations, while staying socially distanced.
There are signs that the steel industry is increasingly embracing this new work culture. In November 2020, Tata Steel announced a ground-breaking ‘Agile Working Model’ for its employees, which allows them to shelter by working from home for up to 365 days a year. Once the pandemic is over the policy will enable employees to work from a location of their choice. The pandemic has helped move away from the traditional thinking of productivity being contingent upon fixed working hours spent within an office environment and opened eyes to the potential of remote working, according to a company spokesperson.2
How OEMs are delivering their services remotely
Although even the “smartest” of factories must retain some staff on-site, it can still be assisted by colleagues working remotely. Previously, it had been normal to keep a team of specialized operators and maintenance engineers, however small, permanently close to the plant. When they were needed to perform specific maintenance tasks, they would be called in to work alongside the regular plant employees to resolve the issue.
However, now that admitting external workers poses a safety risk that could be avoided, some innovative service providers are offering a safe and technology- driven alternative: keep the OEM engineers off-site, but allow contact with the plant staff through advanced audio-visual communication devices.
A powerful example is offered by Tenaris in their hot rolling mill facility in Veracruz, Mexico. The steelmaker reports that it has incorporated new wearable technology to quickly perform maintenance tasks. Helmet-mounted cameras enable audio-visual communications between plant operators and suppliers in real time, without the need for physical proximity. Additionally, the cameras are managed by voice command thus avoiding the necessity to touch them, which further increases safety during complex manual operations. The new technology was first adopted in June 2020, when, due to travel restrictions imposed by the pandemic, a supplier in Italy was unable to support the local team on-site.3
Helmet-mounted cameras are similarly used by Danieli as part of their Q-SPACE connectivity and remote support application. This includes an augmented reality tool that allows a remote expert to take a plant technician through all necessary operations, directly interfacing with the environment being viewed by superimposing illustrative images. This allows delivery of qualified support for equipment maintenance, setup and troubleshooting, while helping to improve operator skills and companies’ know-how.4
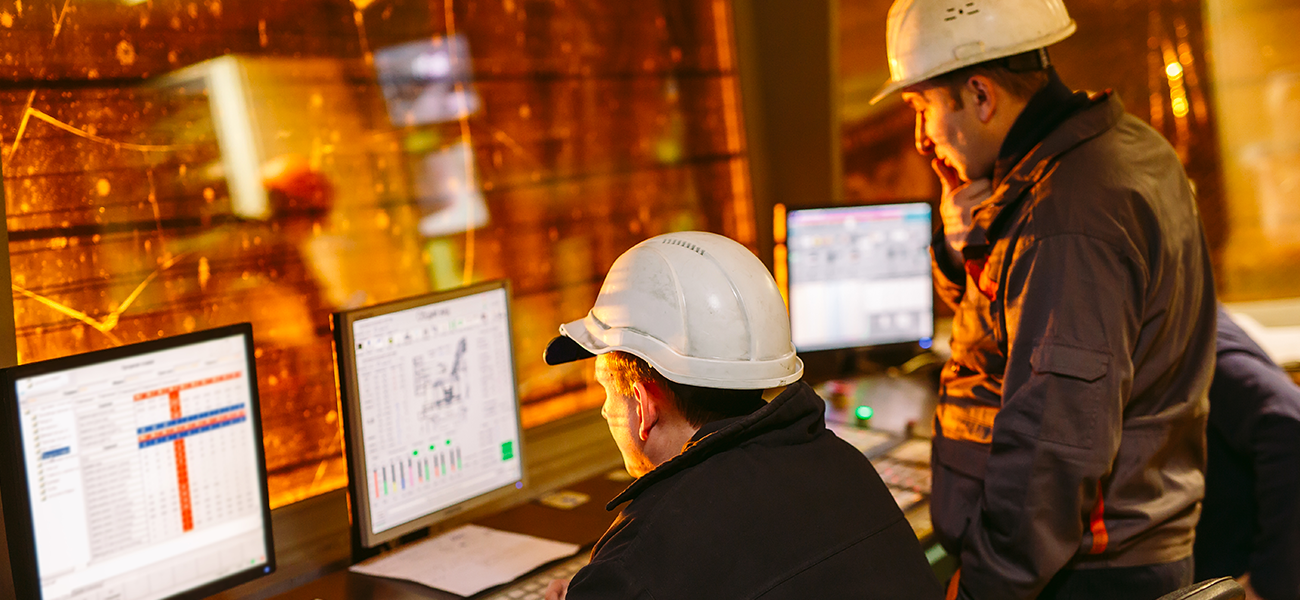
How Steel Hub leverages remote work creatively to help its clients improve operational and financial plant performance
These technical applications present examples how digital technology can facilitate remote working, but remote working can reach even further. Steel manufacturers who benefited from broader specialist assistance before the pandemic now need it more than ever to manage through the recent disruptions. The required expertise can be provided by steel-focused technical consultancies such as Steel Hub, which helps its steel plant clients improve operational performance both technically and financially, and assists them in taking the right capex decisions now to prepare for the opportunities that will arise in the post-COVID period.
At the beginning of the pandemic, Steel Hub’s consultancy services had also been disrupted. Under normal circumstances, Steel Hub’s technical experts spend most of their time in the plants to solve issues hand-in-hand with plant operators and provide technical capability training to the workforce. The pandemic has made this normally-preferred approach temporarily impossible. As such, it has forced Steel Hub to continue innovating its modes of service delivery to ensure that running performance improvement programs can be completed.
As the COVID crisis has made international travel and plant visits either impossible or less practical due to self-quarantine regulations, Steel Hub switched many of its clients to remote support modes. While past discussions typically have taken place on the clients’ shop floors, now increasingly often video conferencing and other means of digital communication are relied upon. Initially this required behavioural changes on both the sides of blue-collar workers and Steel Hub’s veterans, who both were used to working in the plant.
However, the new remote work models quickly revealed their great potential: remote working made it easier for Steel Hub to shift its clients’ attention to deliverables where data-driven analysis and management is superior to carrying out quick (but possibly incomplete) fixes. For instance, in areas such as product quality improvement it is vital that data is analysed properly and standard procedures formulated clearly before action in the plant is taken. Remote work allows even more time than before to elaborate the theoretical foundations of any improvement program. As a side benefit, plant managers’ skills to create and interpret technical reports had to improve, so that technical discussions could be facilitated without presence in the plant. As another benefit, clients seem more motivated to improve the quality of their data management. Furthermore, given Steel Hub experts temporarily cannot instruct operators in the plants, the remote support has forced clients to become more self-reliant in implementing Steel Hub’s recommendations. Ultimately, this has further raised clients’ technical capabilities, who now have to implement instructions provided by Steel Hub experts who normally would carry those out themselves.
As with any crisis, the pandemic exposes the steel industry to serious risks. At the same time, it has accelerated the trend of exploiting digital technology for increasing safety through remote work. This article has presented several examples on how steel plants can be managed and their performance improved without having maintenance engineers or technical consultants such as Steel Hub consultants on-site, instead providing support services remotely.
1 https://fee.org/articles/increased-productivity-is-eliminating-steel-industry-jobs-not-imports/
2 https://www.thehindu.com/business/Industry/tata-steel-announces-new-working-models-for-employees/article33003837.ece
3 https://www.tenaris.com/en/newsroom/news-listing/tenaris-adopts-smart-glasses-to-enhance-operations–04648815620
4 https://www.danieli.com/en/servicenews/q-space-expanded-reality-to-improve-plant-efficiency-and-reduce-opex_46_20.htm