These are stories of businesses like yours, achieving great things
Project Spotlights
Every plant faces unique challenges – and that’s where we come in. This page highlights just a few of the real results we’ve delivered for steelmakers around the world. From solving edge cracking in duplex steel to increasing pickling line efficiency and reducing chromium loss in EAFs, our work is rooted in measurable outcomes. These stories reflect the depth of our technical approach, the trust our clients place in us, and the tangible value we bring to every project.
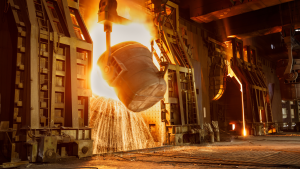
Optimising AOD Chemical Composition of Duplex Stainless Steel
Key Takeaways Problem: A stainless steel producer in Southeast Asia faced quality issues due to non-optimised chemical compositions, leading to frequent casting defects. Challenge: Needed to optimise chemical composition to ensure consistent product quality. Solution: Adjusted desulphurisation and decarburisation steps and proposed SOP modifications for better chemical control. Improvements: Reduced

Optimising EAF Chromium oxide recovery and Oxygen Consumption for Duplex and Ferritic Stainless Steels
Key Takeaways Here are five key takeaways from this document: Problem: A client in Asia faced high oxygen and aluminium consumption in a 140-tonne EAF, leading to chromium losses in slag. Challenge: High operating costs due to inefficient raw material use and chromium losses. Solution: Reviewed and optimised EAF processes,
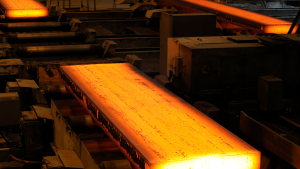
Reducing Longitudinal Depression and Hot Cracking in Duplex Stainless Steel Slabs
Key Takeaways Problem: A stainless steel producer in Asia faced defects in duplex stainless steel slabs due to improper casting parameters and powder formulations. Challenge: Defects led to material loss, reducing yield and disrupting downstream operations. Solution: Identified defect causes, optimised casting settings and powder formulations, and provided staff training.
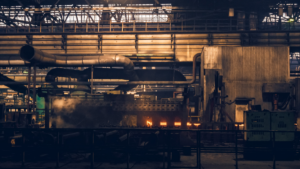
Adjusting Reduction and Tension Patterns of Cold Rolled Steel
Key Takeaways Problem: A steel plant in Southeast Asia faced excessive steel breakages, averaging 8 per day—higher than the benchmark of 5 per day—leading to reduced throughput and increased costs. Challenge: Optimising reduction and tension patterns to improve process stability and product quality. Solution: Conducted a 360° diagnosis, identified reduction
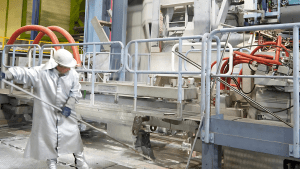
Reducing Dross Formation and Zinc Consumption in Galvanising Line
Key Takeaways Process Optimization is Key – Adjusting operating parameters like temperature profiles and bath chemistry significantly reduced dross formation. Improved Material Handling Reduces Contamination – Better storage and handling of steel coils minimized iron fines and oil contamination, enhancing strip cleanliness. Enhanced Productivity & Cost Savings – Optimized zinc
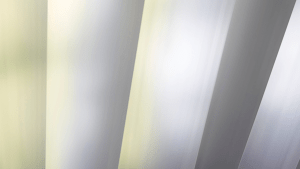
Controlling Spangle Formation During Galvanising process
Key Takeaways Precise Process Control is Essential – Managing zinc bath chemistry, cooling rates, and substrate standards helped achieve consistent spangle formation. Optimised Temperature Management – Adjusting burners to maintain a minimum strip temperature of 500°C improved spangle consistency. Unnecessary Additives Eliminated – Removing 53 metric tonnes of tin annually
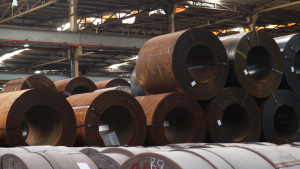
Optimising Pickling Line Conditions to Increase Efficiency
Key Takeaways Process Optimisation – Addressing inconsistencies in pickling improved overall efficiency and steel quality. Chemical Control – Regulating chloride levels and stabilising HCl, iron, and pH prevented over-pickling. Temperature Management – Better control reduced material inconsistencies before cold rolling. Quality Tracking & Training – Implementing staff training and monitoring
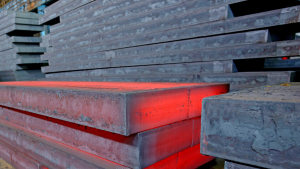
Addressing Edge Crack Issues in Duplex Stainless Steel during Hot Rolling
Key Takeaways Comprehensive Process Analysis – A systematic review of the hot rolling process identified key factors contributing to edge cracking in duplex stainless steel plates. Enhanced Product Quality – Improved slab handling, including edge chamfering, significantly reduced edge cracks and improved final product quality. Optimised Chemical Composition – Adjusting
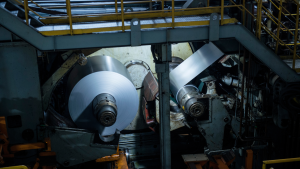
Reducing Steel Breakages and production stoppages in a cold rolling mill plant
Key Takeaways Problem: Frequent strip breakages and stoppages in a Bangladesh cold rolling mill. Diagnosis: 360° assessment identified process and procurement issues. Solution: Optimised rolling patterns, lubrication, and roll specifications. Enhancements: Improved pickling line and implemented alternative roll sourcing. Impact: +30% productivity, USD 35M revenue increase, 3 new SOPs approved.
Project Case Studies
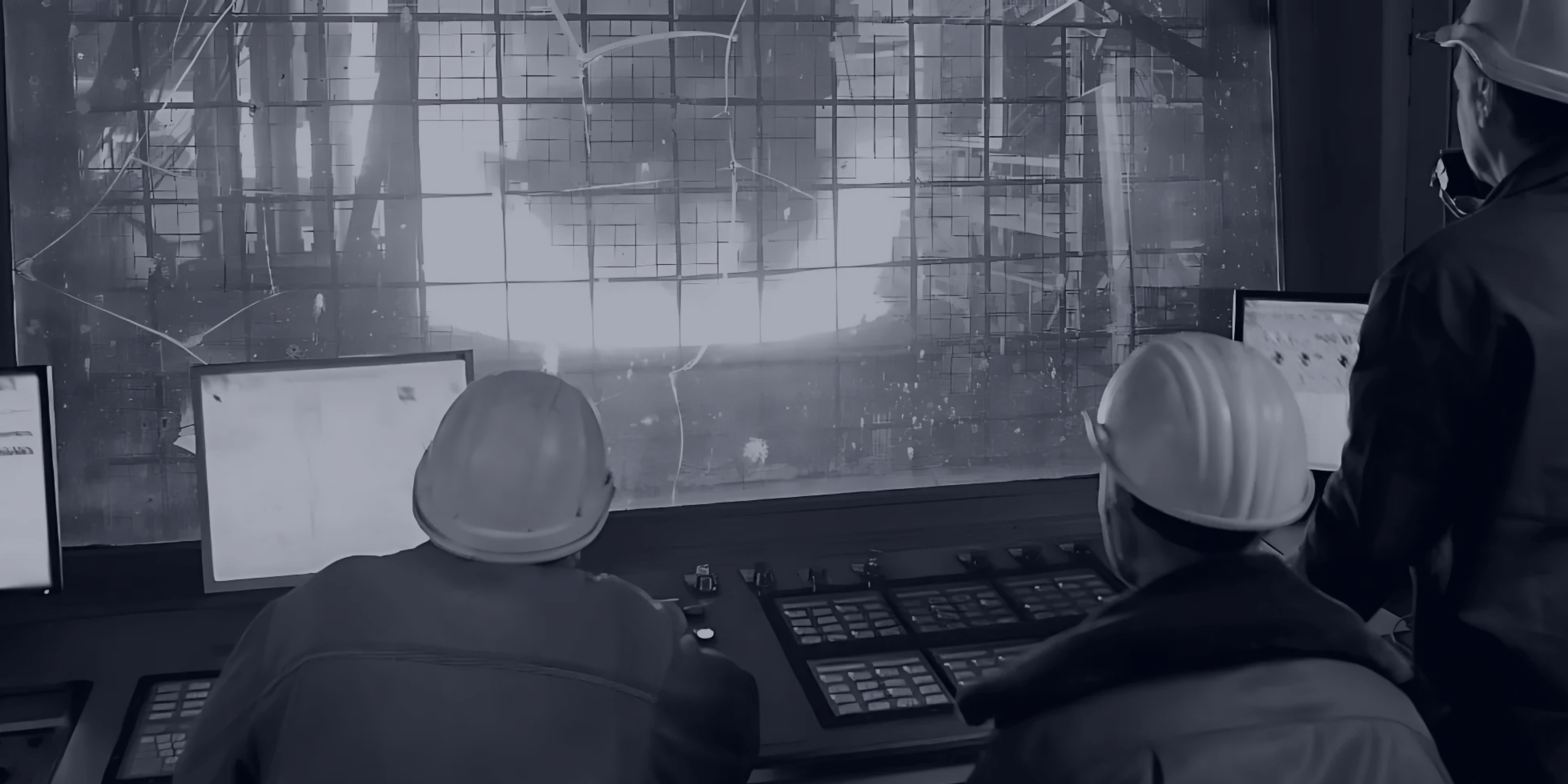
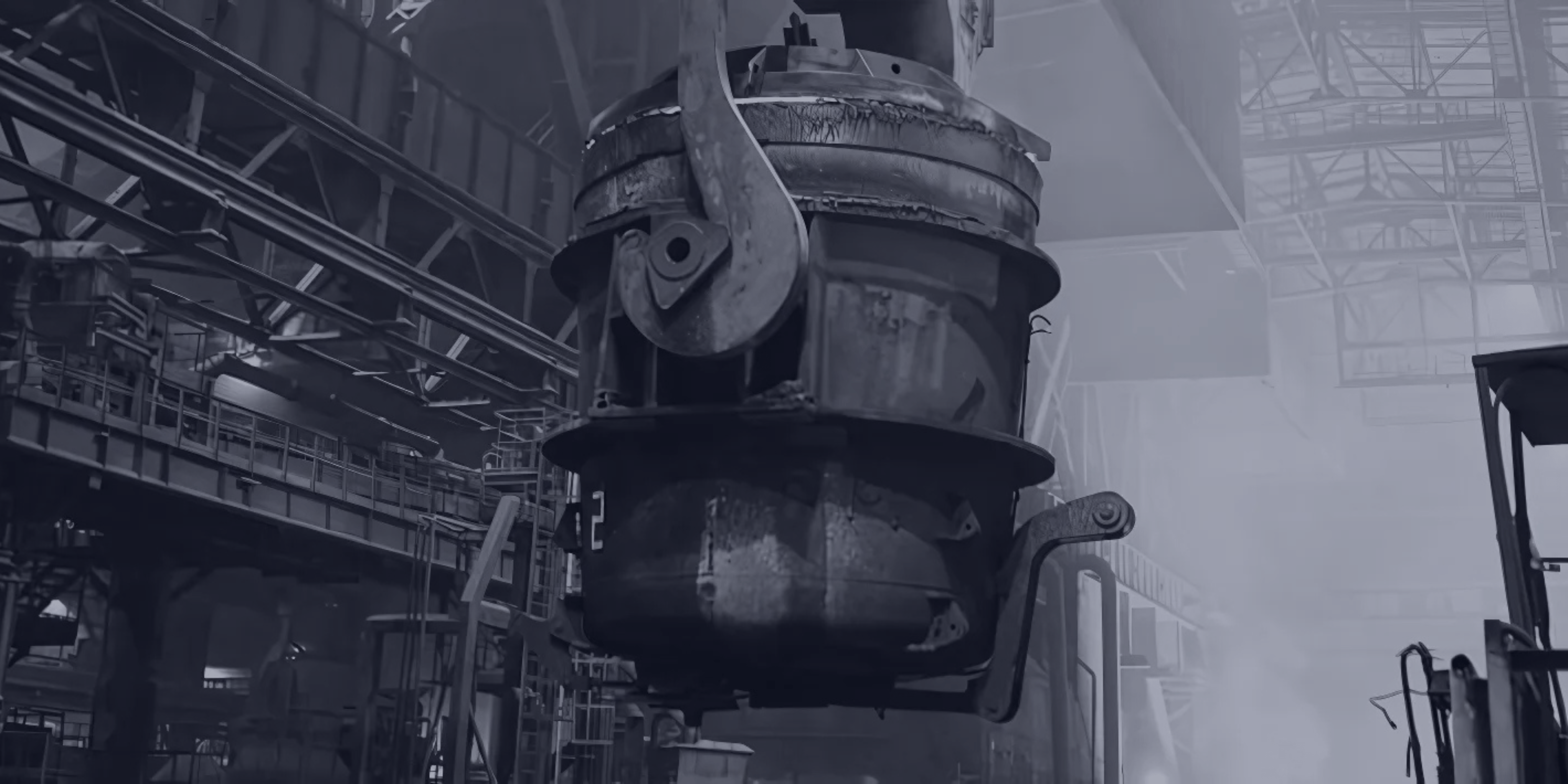
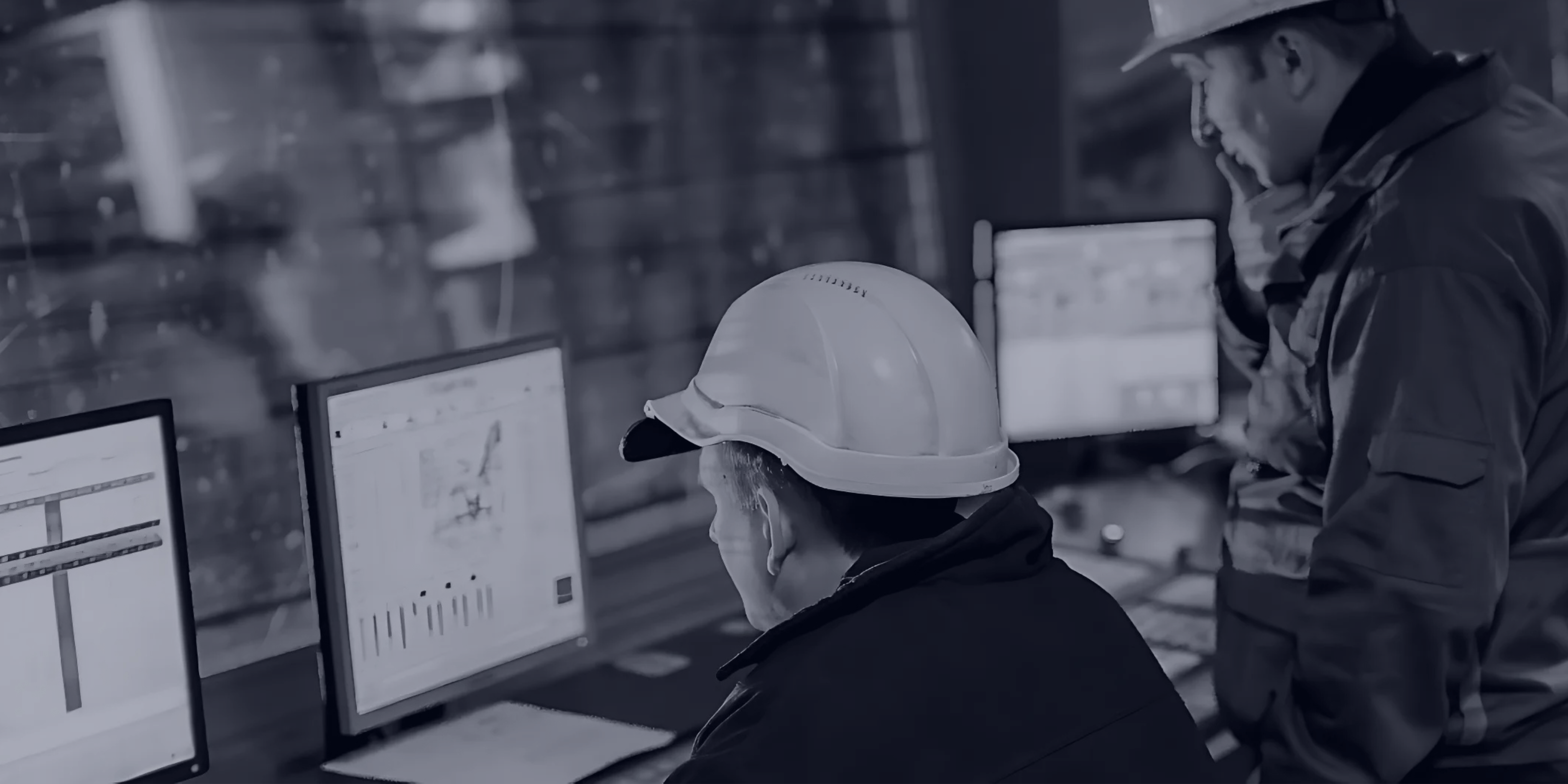
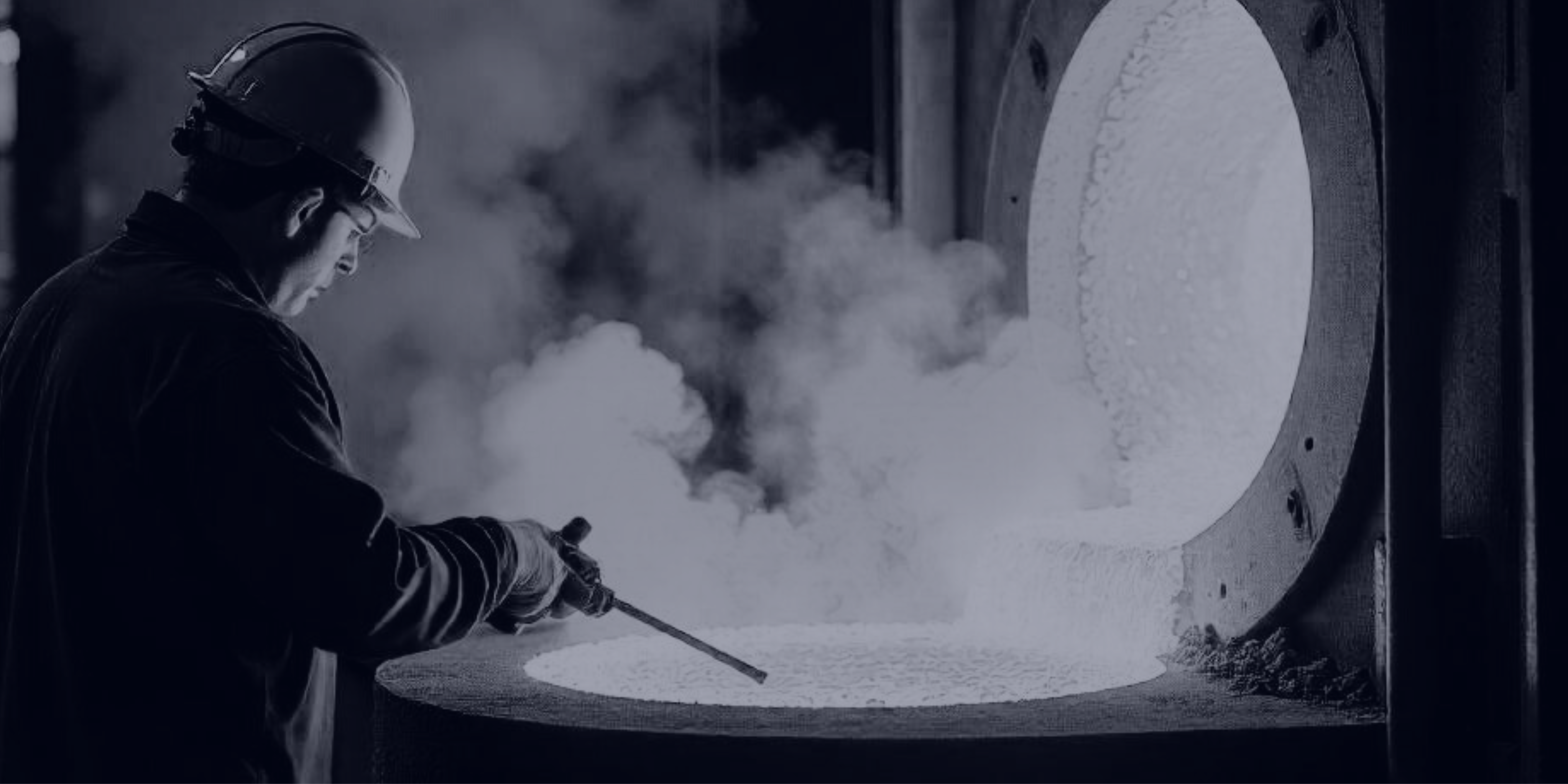
Operational excellence program at an Eastern European steel plant
Increasing yield by 15% with less than 1 million USD of capital expenditure
Operational excellence in refractory materials management at a mini mill
Reducing refractory costs by over 30% per annum, saving more than 1.1 million USD yearly
Energy efficiency program at a European mega steel plant
Cutting electricity costs by 13% annually - saving 36 million € and boosting profit margins
Operational Due Diligence of two Celsa EAF Steel Plants in the UK and Norway
Enabling a successful acquisition by identifying key risks, CAPEX needs, and decarbonisation potential
Stay Informed with Our Newsletter
Get exclusive insights, industry trends, and expert updates- delivered straight to your inbox!